Контроль качества при производстве гидравлических систем ООО «ПНЕВМАКС»
24.05.2021
Сазанов А. И., начальник производства ООО «ПНЕВМАКС»
Современный гидравлический привод объемного действия – это совокупность сложных высокотехнологичных устройств, узлов и агрегатов. Проектирование и производство гидравлических систем требует особого подхода, ведь именно от качественного исполнения напрямую зависит надежность и срок эксплуатации гидравлического привода. Конъюнктура рынка такова, что заказчику часто необходимо однократно решить задачу, то есть, изготовить систему нужно в единственном экземпляре. В случае единичного производства особенно сложно получить гарантированно качественный результат.
Компания «ПНЕВМАКС» успешно проектирует и производит гидравлические приводы и их составные части, гарантируя стабильно высокое качество производства для мелкосерийных и даже единичных заказов. Это становится возможным благодаря ориентации всей компании, от руководства до конечного исполнителя, на обеспечение высоких стандартов качества выпускаемой продукции. В структуре компании организовано подразделение, основной задачей которого является контроль над исполнением заказов, а именно выдерживанием сроков на всех этапах жизненного цикла проекта и соблюдением всех особых условий и требований.
Отдел закупок компании ведет тщательный отбор поставщиков, тесно взаимодействуя со службой входного контроля. Это дает возможность контролировать добросовестность поставщиков, и при необходимости принимать превентивные меры. Предъявляя высокие требования к себе, «ПНЕВМАКС» требует соответствия этим требованиям и от своих партнеров, как за рубежом, так и в России. Логисты компании разрабатывают наиболее быстрые и эффективные способы доставки комплектующих, а на складах созданы все условия для обеспечения их правильного приема и хранения, поддерживаются необходимые температура, влажность и чистота. Автоматизированная система адресного хранения не только позволяет исключить человеческий фактор при комплектации заказов на складе, но и обеспечивает соблюдение принципа «первый пришёл, первый ушел».
Единичное производство невозможно без индивидуального проектирования каждого заказанного изделия, разработки и подготовки технологического процесса. Безусловно, это требует больших временных затрат, которые зачастую просто не предусмотрены заказчиком в графике реализации проекта. Для сокращения сроков поставки широко применяются гибкие модульные решения, которые разработаны конструкторско-технологическими службами предприятия, а надежность их подтверждена опытной эксплуатацией. На этапе конструкторской подготовки предпочтение отдается решениям, отвечающим принципам «нулевой ошибки» на производстве. Таким образом, сокращается время, затрачиваемое как на выполнение производственных операций, так и на контроль. Все эти меры не только сокращают срок подготовки конструкторской документации для согласования с заказчиком, но и, в конечном итоге, минимизируют время, необходимое для запуска изделия в производство.
Большое внимание конструкторы уделяют эргономике и ремонтопригодности проектируемого оборудования, что важно для специалистов-механиков. В установках, предназначенных для непосредственной работы операторов, акцент делается на современные требования к интерфейсу «человек-машина».
Система наставничества, применяемая в компании в комплексе с проведением периодических внутренних аттестаций персонала, гарантирует формирование у исполнителей высокого уровня ответственности за выполняемую работу, и, как следствие, обеспечивает высокое качество результата. Каждое рабочее место оснащено необходимым набором средств контроля, а каждый исполнитель обучен методикам проверки.
Чистота – это важнейший фактор надежности гидравлических устройств. Даже незначительные механические загрязнения, которые рабочая жидкость разносит по системе, могут привести к поломке и остановке всего оборудования. И даже если повреждение не наступило в течение короткого времени, вероятность возникновения проблемы остается довольно высокой. Очистка рабочей жидкости и гидросистемы в целом – сложный и дорогостоящий процесс. Поэтому очень важно предупредить саму возможность загрязнения. Все детали после механической обработки проходят финишную доводку и устранение заусенцев, после чего подвергаются автоматизированной мойке под давлением. Для защиты внутренней поверхности баков от коррозии применяется система двухкомпонентного эпоксидного маслостойкого покрытия, расслаивание которого в результате воздействия рабочей жидкости гидросистемы исключено. Зонирование «грязных» зон механической обработки от чистых сборочных и испытательных участков, проведение влажной уборки четыре раза за рабочую смену исключают возможность засорения продукции.
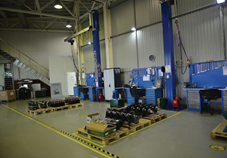
При проектировании систем автоматизированного управления пристальное внимание уделяется соблюдению всех требований ПУЭ и отраслевых стандартов. В электромонтаже применяется аппаратура, отвечающая самым высоким требованиям, а для разводки по оборудованию используются кабели исключительно в маслостойкой полиуретановой оболочке.
Участки испытаний и контроля качества оснащены необходимым набором поверенных средств измерений, в том числе, системой контроля и испытаний с компьютерным управлением.
Вся производимая компанией продукция проходит 100% выходной контроль, по результатам которого заполняется протокол контроля качества. Его заверенная копия прикладывается к паспорту изделия. Только после положительного результата контроля изделию присваивается индивидуальный заводской номер и наносится соответствующая маркировка. Таким образом, передача на склад продукции, не прошедшей контроль, исключена.
В 2019 году персонал сварочного производства компании успешно прошел добровольную сертификацию НАКС в отношении ручной и полуавтоматической сварки трубопроводов и строительных конструкций особо ответственных технических устройств, относящихся к категории опасных. Это еще раз подтверждает стремление предприятия к обеспечению стабильно высокого уровня качества.
Продукция компании получила сертификат о происхождении товара по форме СТ1, подтверждающий производство продукции на территории Российской Федерации. Это гарантирует заказчикам оперативную и профессиональную техническую поддержку не только на этапе поставки, но и на всех этапах жизненного цикла продукции. При необходимости всегда на связи с заказчиком специалисты по наладке и монтажу, технической поддержке и конструкторского отдела. Для ООО «ПНЕВМАКС» очень важна обратная связь от наших заказчиков по опыту эксплуатации произведенного компанией оборудования. Информация тщательно собирается и анализируется службой качества. По результатам этой работы проводятся корректирующие мероприятия в соответствующих подразделениях.
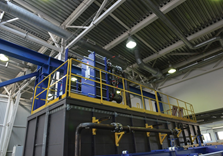
Компания «ПНЕВМАКС» всегда открыта для диалога со своими клиентами. Наши специалисты готовы помочь в области технического аудита и всесторонних технических консультаций по вопросам эксплуатации оборудования.
Профессионализм сотрудников и качество продукции «ПНЕВМАКС» подтверждено многолетним сотрудничеством с промышленными гигантами нашей страны, среди которых ПАО «Северсталь», ПАО «КАМАЗ», ПАО «Магнитогорский металлургический комбинат», ПАО «НЛМК», АО «УТЗ», ПАО «Силовые машины», ПАО «Уралмашзавод, ОАО «Тяжмехпресс», ОАО «ПФ «КМТ» и другие.
Современный гидравлический привод объемного действия – это совокупность сложных высокотехнологичных устройств, узлов и агрегатов. Проектирование и производство гидравлических систем требует особого подхода, ведь именно от качественного исполнения напрямую зависит надежность и срок эксплуатации гидравлического привода. Конъюнктура рынка такова, что заказчику часто необходимо однократно решить задачу, то есть, изготовить систему нужно в единственном экземпляре. В случае единичного производства особенно сложно получить гарантированно качественный результат.
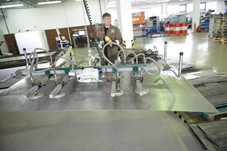
Отдел закупок компании ведет тщательный отбор поставщиков, тесно взаимодействуя со службой входного контроля. Это дает возможность контролировать добросовестность поставщиков, и при необходимости принимать превентивные меры. Предъявляя высокие требования к себе, «ПНЕВМАКС» требует соответствия этим требованиям и от своих партнеров, как за рубежом, так и в России. Логисты компании разрабатывают наиболее быстрые и эффективные способы доставки комплектующих, а на складах созданы все условия для обеспечения их правильного приема и хранения, поддерживаются необходимые температура, влажность и чистота. Автоматизированная система адресного хранения не только позволяет исключить человеческий фактор при комплектации заказов на складе, но и обеспечивает соблюдение принципа «первый пришёл, первый ушел».
Единичное производство невозможно без индивидуального проектирования каждого заказанного изделия, разработки и подготовки технологического процесса. Безусловно, это требует больших временных затрат, которые зачастую просто не предусмотрены заказчиком в графике реализации проекта. Для сокращения сроков поставки широко применяются гибкие модульные решения, которые разработаны конструкторско-технологическими службами предприятия, а надежность их подтверждена опытной эксплуатацией. На этапе конструкторской подготовки предпочтение отдается решениям, отвечающим принципам «нулевой ошибки» на производстве. Таким образом, сокращается время, затрачиваемое как на выполнение производственных операций, так и на контроль. Все эти меры не только сокращают срок подготовки конструкторской документации для согласования с заказчиком, но и, в конечном итоге, минимизируют время, необходимое для запуска изделия в производство.
Большое внимание конструкторы уделяют эргономике и ремонтопригодности проектируемого оборудования, что важно для специалистов-механиков. В установках, предназначенных для непосредственной работы операторов, акцент делается на современные требования к интерфейсу «человек-машина».
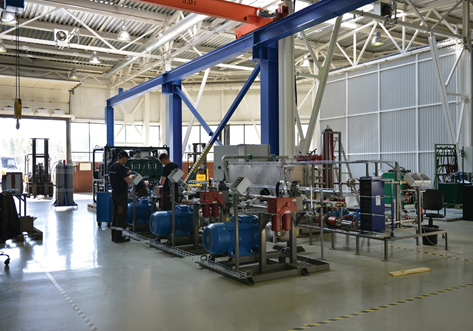
Чистота – это важнейший фактор надежности гидравлических устройств. Даже незначительные механические загрязнения, которые рабочая жидкость разносит по системе, могут привести к поломке и остановке всего оборудования. И даже если повреждение не наступило в течение короткого времени, вероятность возникновения проблемы остается довольно высокой. Очистка рабочей жидкости и гидросистемы в целом – сложный и дорогостоящий процесс. Поэтому очень важно предупредить саму возможность загрязнения. Все детали после механической обработки проходят финишную доводку и устранение заусенцев, после чего подвергаются автоматизированной мойке под давлением. Для защиты внутренней поверхности баков от коррозии применяется система двухкомпонентного эпоксидного маслостойкого покрытия, расслаивание которого в результате воздействия рабочей жидкости гидросистемы исключено. Зонирование «грязных» зон механической обработки от чистых сборочных и испытательных участков, проведение влажной уборки четыре раза за рабочую смену исключают возможность засорения продукции.
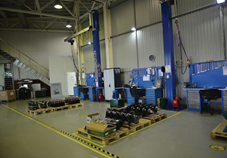
При проектировании систем автоматизированного управления пристальное внимание уделяется соблюдению всех требований ПУЭ и отраслевых стандартов. В электромонтаже применяется аппаратура, отвечающая самым высоким требованиям, а для разводки по оборудованию используются кабели исключительно в маслостойкой полиуретановой оболочке.
Участки испытаний и контроля качества оснащены необходимым набором поверенных средств измерений, в том числе, системой контроля и испытаний с компьютерным управлением.
Вся производимая компанией продукция проходит 100% выходной контроль, по результатам которого заполняется протокол контроля качества. Его заверенная копия прикладывается к паспорту изделия. Только после положительного результата контроля изделию присваивается индивидуальный заводской номер и наносится соответствующая маркировка. Таким образом, передача на склад продукции, не прошедшей контроль, исключена.
В 2019 году персонал сварочного производства компании успешно прошел добровольную сертификацию НАКС в отношении ручной и полуавтоматической сварки трубопроводов и строительных конструкций особо ответственных технических устройств, относящихся к категории опасных. Это еще раз подтверждает стремление предприятия к обеспечению стабильно высокого уровня качества.
Продукция компании получила сертификат о происхождении товара по форме СТ1, подтверждающий производство продукции на территории Российской Федерации. Это гарантирует заказчикам оперативную и профессиональную техническую поддержку не только на этапе поставки, но и на всех этапах жизненного цикла продукции. При необходимости всегда на связи с заказчиком специалисты по наладке и монтажу, технической поддержке и конструкторского отдела. Для ООО «ПНЕВМАКС» очень важна обратная связь от наших заказчиков по опыту эксплуатации произведенного компанией оборудования. Информация тщательно собирается и анализируется службой качества. По результатам этой работы проводятся корректирующие мероприятия в соответствующих подразделениях.
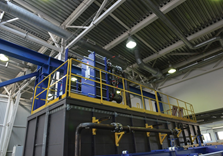
Компания «ПНЕВМАКС» всегда открыта для диалога со своими клиентами. Наши специалисты готовы помочь в области технического аудита и всесторонних технических консультаций по вопросам эксплуатации оборудования.
Профессионализм сотрудников и качество продукции «ПНЕВМАКС» подтверждено многолетним сотрудничеством с промышленными гигантами нашей страны, среди которых ПАО «Северсталь», ПАО «КАМАЗ», ПАО «Магнитогорский металлургический комбинат», ПАО «НЛМК», АО «УТЗ», ПАО «Силовые машины», ПАО «Уралмашзавод, ОАО «Тяжмехпресс», ОАО «ПФ «КМТ» и другие.